山一ハガネの提案力・技術力でお客様の「潜在的な課題」をお客様と共に解決-株式会社南信精機製作所様
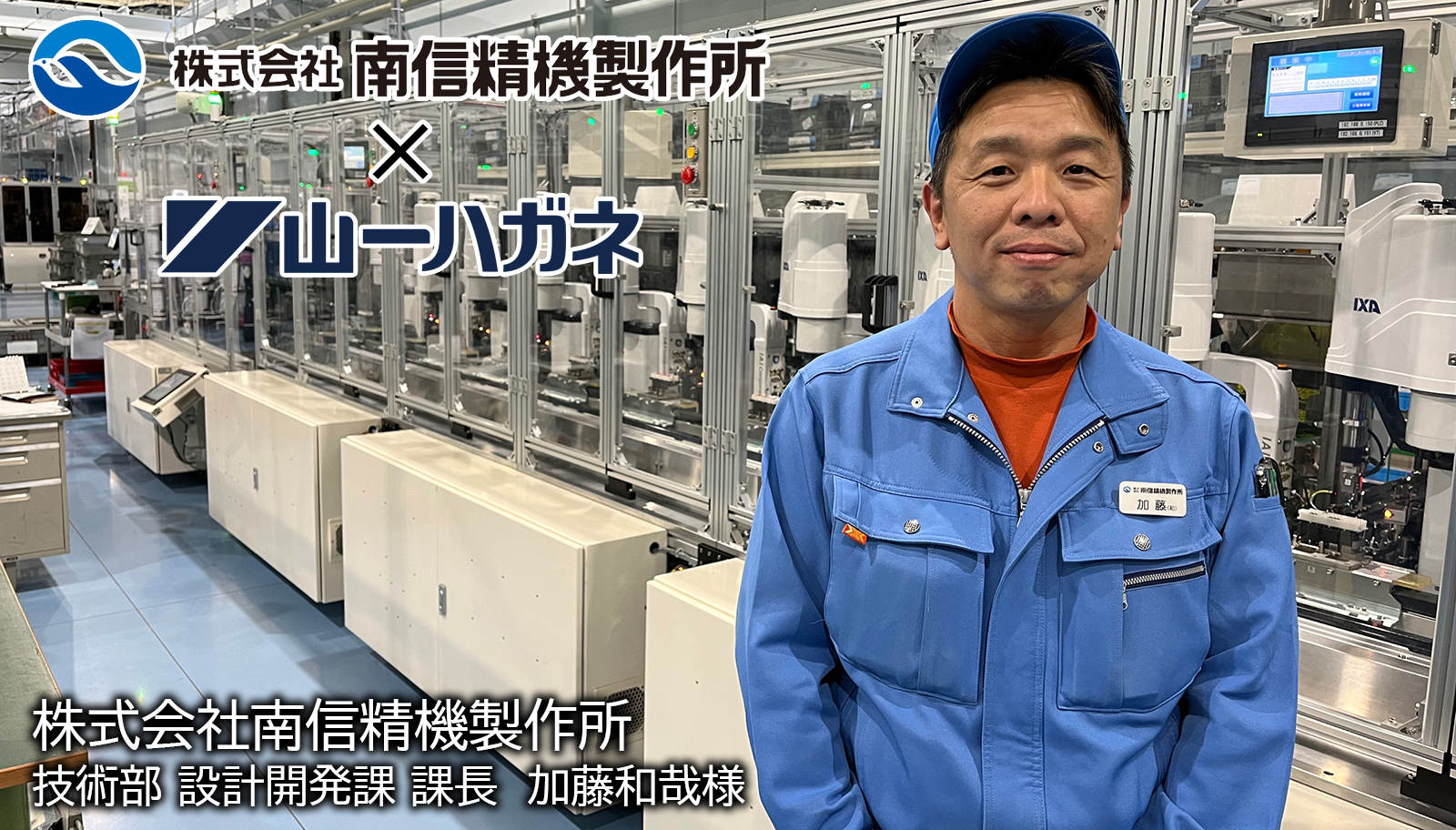
■株式会社南信精機製作所様概要
・設立:1960年4月
・事業内容:
精密プレス製品の製造・販売
精密プラスチック製品の製造・販売
金属+樹脂の複合製品の製造・販売
プレス金型・プラスチック金型の設計・製作
生産・検査設備の設計・製作
・従業員数:230名
・南信精機製作所様のHP→
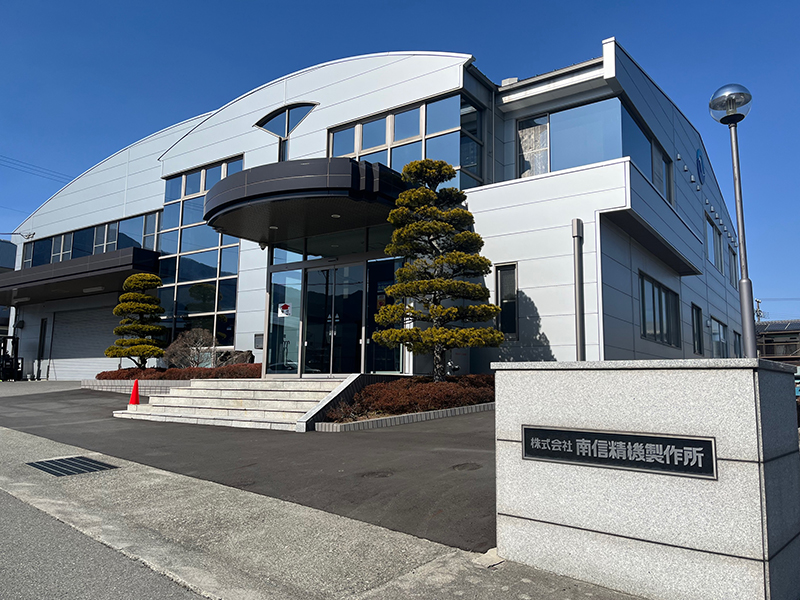
南アルプスと中央アルプスの狭間、長野県飯島町にある電子部品メーカー株式会社南信精機製作所様。
同社では、精密プレス、精密プラスチック、インサート・アウトサート成形、さらに相互のメリットを合わせた独自の「プレスチックス」を武器に、車載部品や整流子など多彩な部品の開発・製造を手がけている。他社に追随を許さない特徴のひとつが、開発から設計・量産・品質保証までをトータルで手掛ける「一貫生産体制」だ。また、製品のみならず、金型から、生産に使用される専用機に至るまでを社内で製作できるのも強み。品質、納期、コスト削減など様々な優位性をもとに、お客様にとって付加価値の高い製品でニーズを的確に捉え、躍進を続けている。
■南信精機製作所様のAM(Additive Manufacturing)技術活用
自動車業界においてコスト削減や品質の安定化を目的とした部品の共通化が進むなか、サプライヤーには大ロットへの対応が求められている。一般的に大ロット=金型技術だが、金型製作において従来の加工では理想的な構造を設けることが難しいものがあり、部品形状によっては生産効率を上げられないこともあった。
そこで同社が着目したのが金属3Dプリンタ。3Dプリンタなら自由な構造が実現できるため、今までは金型化が難しかった部品についても生産効率を上げられるのではないかと考え、金属3Dプリンタによる金型部品製造の検証がスタートした。
■金属3Dプリンタによる金型部品製作で見えた課題
同社の製品の多くは車載関連部品で、ECU等に使用される中継器やコネクタ等の機能部品だ。1μm単位の非常に厳しい寸法精度が要求されるため、設備、加工業者、形状による相違を検証する必要があり、製造5社に依頼、加工精度の比較を実施された。
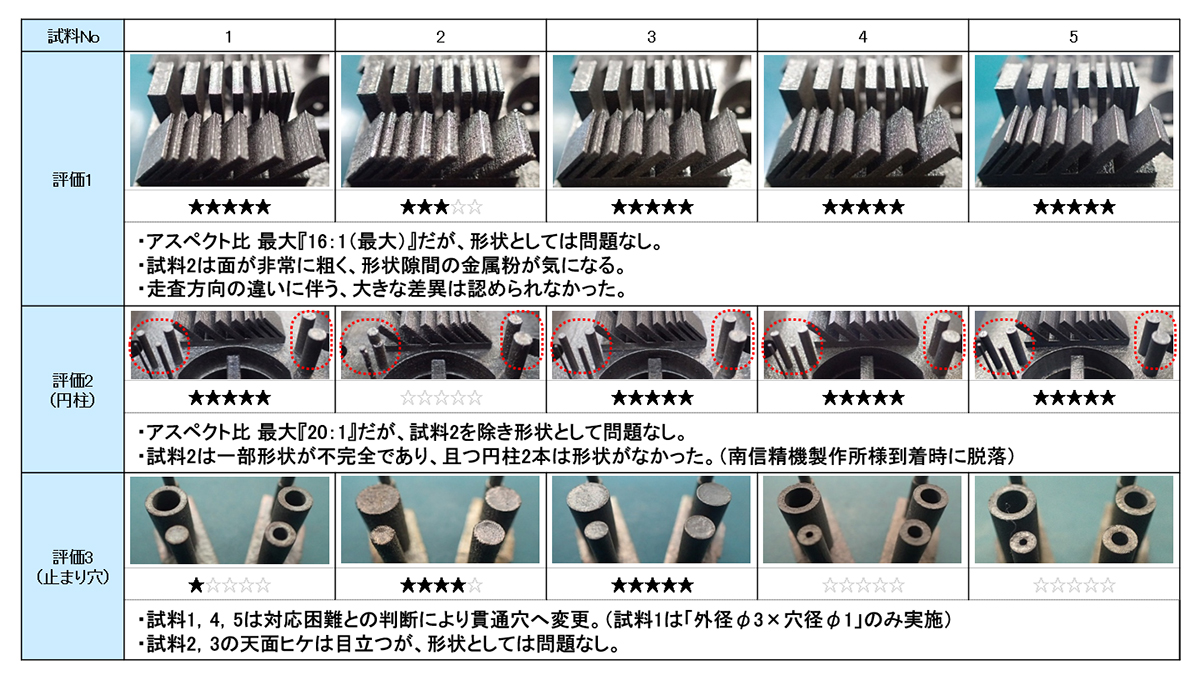
<検証により見えた課題>
- 加工設備および加工者により、品質レベルは大きく異なる。
- いずれも専業企業に製作依頼しているが、設備および加工者の選定基準が分からず不安が残る。
- 部品加工終盤にAM加工不具合を発見した場合、納期面への影響は必至。よって、設備および業者選定は極めて重要である。
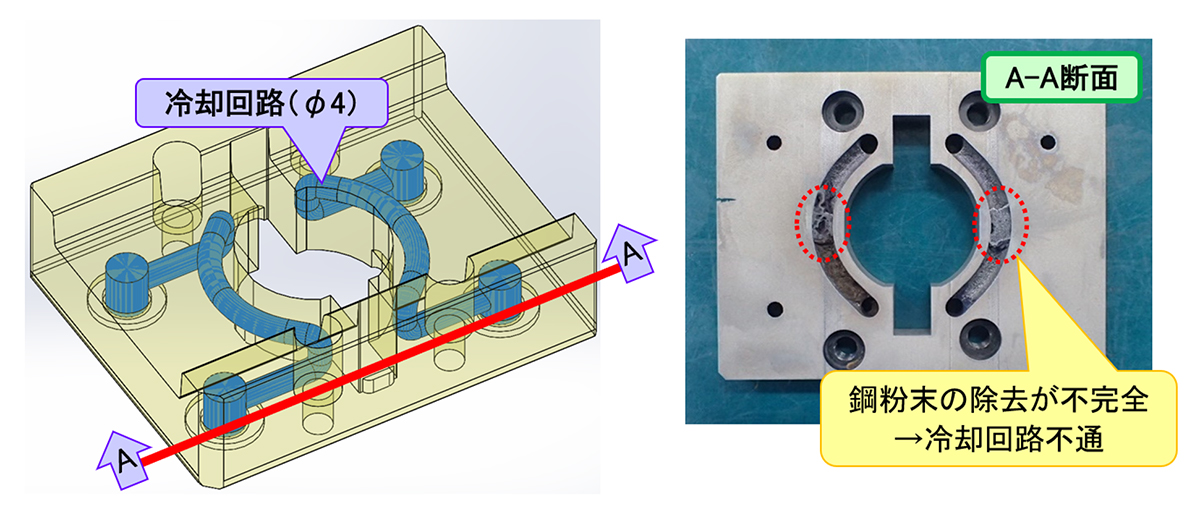
現時点において、金属3Dプリンタの造形物は採算が見込めない点も多く、実用に向けたハードルは高い。
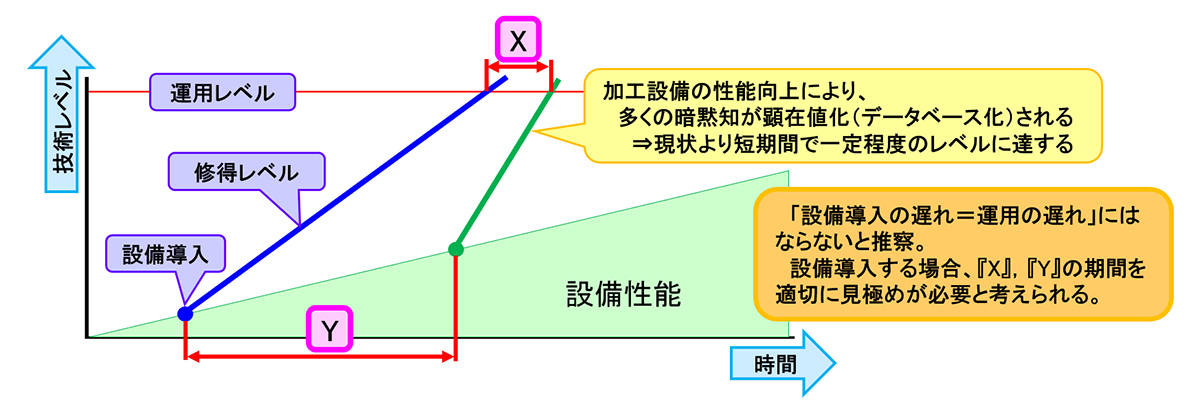
このような状況のなか、とある3Dプリンタ関連の展示会で講師として招かれた加藤様が、同じく講師として招かれた山一ハガネの小林祐太と出会った。
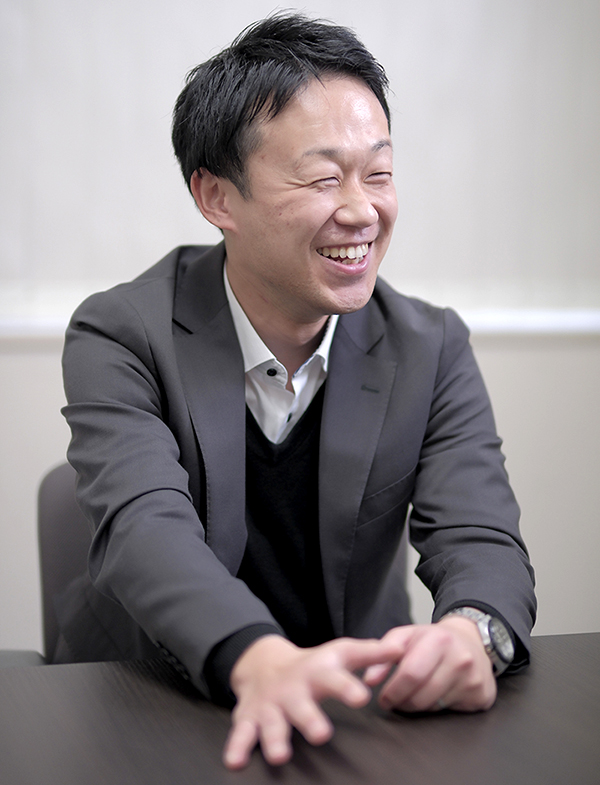
事業開発Sec.マネージャーの小林祐太
■お客様の“潜在ニーズ”に応える山一ハガネの提案型営業
展示会の縁で情報交換を進めるなかで、山一ハガネの持つ技術・製品で南信精機製作所様のお役に立つことができると小林は確信。すぐに同社へ訪問し、高度に自動化された工場内を隅々まで見学。ほとんどがアルミの材料でできている自動機を見て、山一ハガネの形状最適化技術と高精度樹脂3Dプリンタの造形技術で、現場の利便性向上=生産性向上に役立てるのではないかと考えた。
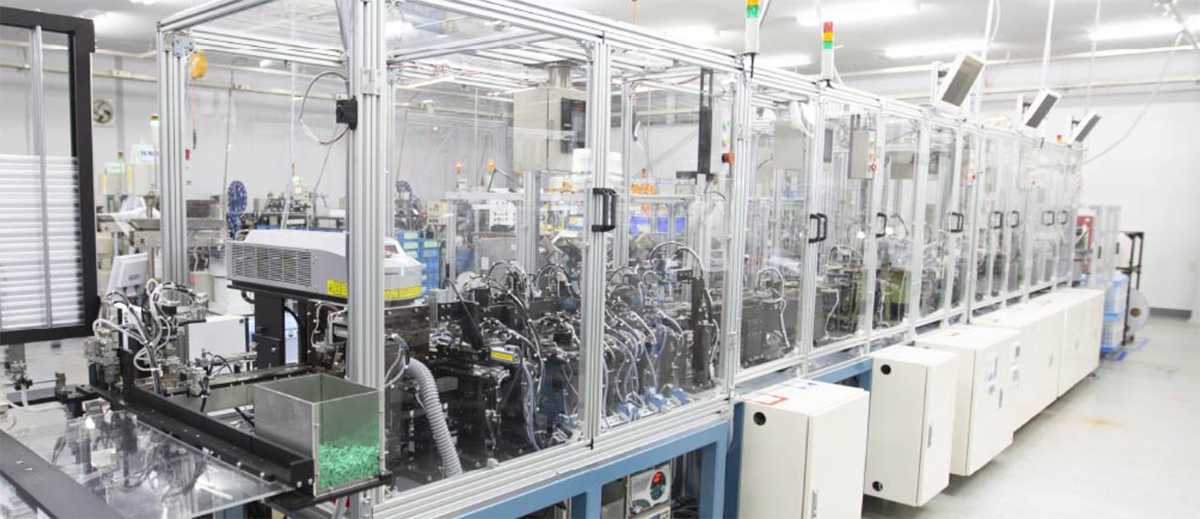
そこでまず提案したのが、山一ハガネで製作実績があった「取り出しハンド」だった。南信精機製作所様の現場において、特に取り出しハンドで“困りごと”があった訳ではなかったが、生産性向上につながる可能性には興味を持たれた。生産性の向上は、製造の現場において永遠の課題である。
「お客様から“困りごと”を相談されてから動いていては遅いのです。お客様が望むものを作っていても付加価値は高くならない。山一ハガネは“付加価値の創造”でお客様の役に立つことが使命と考えています。お客様自身も認識していない『潜在的なニーズ』に応える商品・サービスの提供こそ山一ハガネの価値なのです。」そう小林は熱く語る。
■樹脂3Dプリンタの固定観念を覆した山一ハガネの造形技術
金属3Dプリンタでは高い知見をお持ちの加藤様だが、樹脂3Dプリンタのことはあまり関心が無かったという。なぜなら、樹脂の3Dプリンタ製品は強度に課題があると思っていたため、そもそも現場で活用する発想自体が無かったのである。
先述の金属3DプリンタでAMのモノづくりのハードルを感じていた状況もあり、小林からの提案を面白いと感じていただけた。こうして、南信精機製作所様と山一ハガネによる自動機への樹脂製3Dプリンタ製品導入プロジェクトがスタートした。
そこで活きたのが山一ハガネの形状最適化技術と3Dプリンタの造形技術だ。
試作一号機から強度としては十分なものができた。これには加藤様も驚いたという。
「樹脂は強度に課題があるという固定観念を山一ハガネさんが覆してくれました。また、形状最適化により、強度だけでなく配線の取り回しでも既存の製品より優れており、利便性向上につながっています。」そう笑顔で語る加藤様。しかしながら課題もあった。金属と比べ樹脂は弾性率が高すぎたのである。その結果“揺れ”が起きてしまい、取り出した部品が落ちてしまうという現象が起こった。「強度には自信があり、その要件は満たしていたのですが…弾性率の問題は実際に機械で動かすまで分かりませんでした。」と苦笑する小林。
取り出しハンドの試作一号機。弾性率が高すぎて“揺れ”が起きている
両社が協力してこの課題を改善した二号機では、見事に“揺れ”を克服。実際のラインで使えるものができた。今後、南信精機製作所様の新規ライン立ち上げの際にこの取り出しハンドが装着された自動機が稼働する予定である。
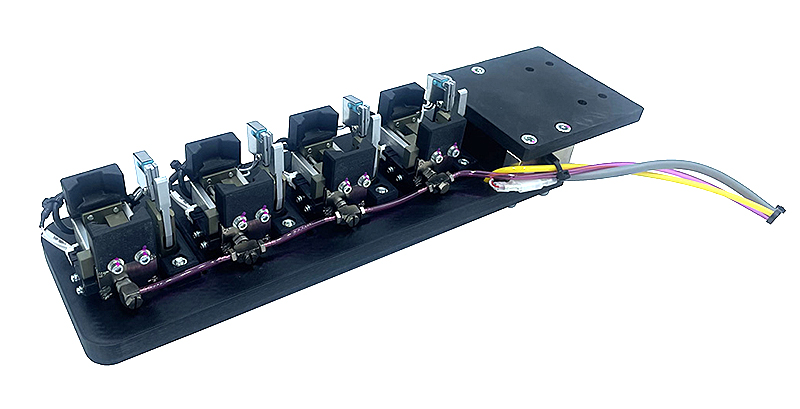
完成した取り出しハンド二号機。見事に“揺れ”を克服
「樹脂は軽量化が可能なため、大型化できるところにメリットを感じます。特に道具や治具を作るのには向いており、一品物を作るのは本当に適していると今回のモノづくりを通じて感じました。」と加藤様も樹脂3Dプリンタの可能性を評価した。
■AMファクトリーモールがお客様の潜在的な困りごとを可視化
加藤様の「樹脂3Dプリンタの固定観念」を覆すことができたのは、山一ハガネが誇る「AMファクトリーモール」の存在だ。
山一ハガネには、材料となるフィラメント製造から、設計、自社製3Dプリンタによる高品質な造形、さらに塗装とレーザー刻印の加飾技術までを“一気通貫”で行える社内体制がある。

このような樹脂3Dプリンタの“一気通貫”のモノづくりができる会社は、日本では山一ハガネだけだ。
そのため、山一ハガネの営業は材料から設計、製造、加飾まで、高い知見を持つ。その営業自らがお客様の現場に行き、お客様と同じ光景を見て、観察して、体験する。そこでこだわるのは“お客様が取り組もうとしている工程全体を見渡して最適化すること”だ。一部の工程内での部分最適化にとどめず、全体最適を見越してお客様と話すことで、お客様も気が付いていなかった“潜在的な困りごと”が見えてくる。
だからこそ、現場の潜在的な課題解決について、今までにない方法で提案できるのだ。
「“あるべき姿”をご提案することでお客様との信頼関係を構築し、山一ハガネと仕事をすればモノづくりがうまくいくと感じて貰えたら嬉しい。」そう小林は熱く語る。その分、幅広い分野での知見が営業に求められるのは言うまでもない。
■今後の展開について
今回の取り出しハンド開発を通じて樹脂3Dプリンタ製品の可能性を実感した南信精機製作所様。徹底して現場のアイデアを活かすことにこだわっている同社らしく、すでに次の展開も視野に入れている。
「当社の思いは“Made by 南信精機製作所”。当社でないとできないモノづくりを目指しており、規定路線ではなく、常に新しさを追及しています。失敗してもいい、なぜ失敗したかを考える。失敗したプロセスの理解が深まれば、成功するためのプロセスを得られる。そして違うプロジェクトに挑戦して成功すればいい。これが当社の思いです。3Dプリンタは新しい技術。新しい技術を使いこなすには自分たちで動かないといけないが、それには限界がある。山一ハガネさんは新しい要素技術を提供してくださるので、当社も新しいことにチャレンジできるのです。」と胸を張る加藤様。
その言葉を受け小林も「今まで当たり前だった作業や工程の中で発生する課題の中には、本来であれば課題になるが時間的な制約で大きな課題として取り扱えなかった“見て見ぬふり”をしていたものが沢山あります。しかし、よりDX中心でモノづくりの変革が必要とされる今だからこそ、FA(ファクトリーオートメーション)や生産設備でも“共創”による改革を起こしたい。こういった思いに共感していただけた南信精機製作所様のような企業様と新たな共創を起こし、中小企業同士のネットワークを構築して諸外国には負けない日本ならではの技術創出をしたいです。」とモノづくりの未来を語る。
南信精機製作所様と山一ハガネの“共創”による現場の変革はこれからも続いていく。
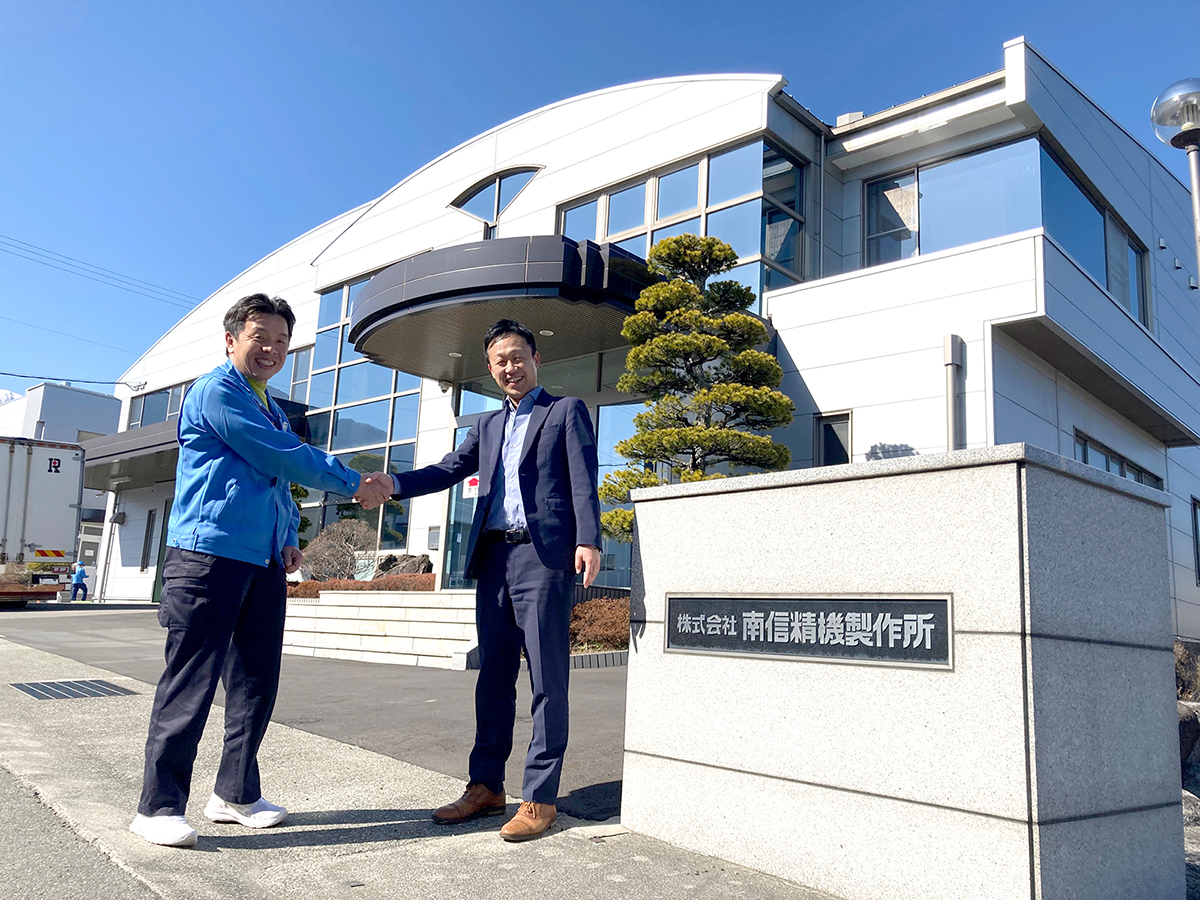
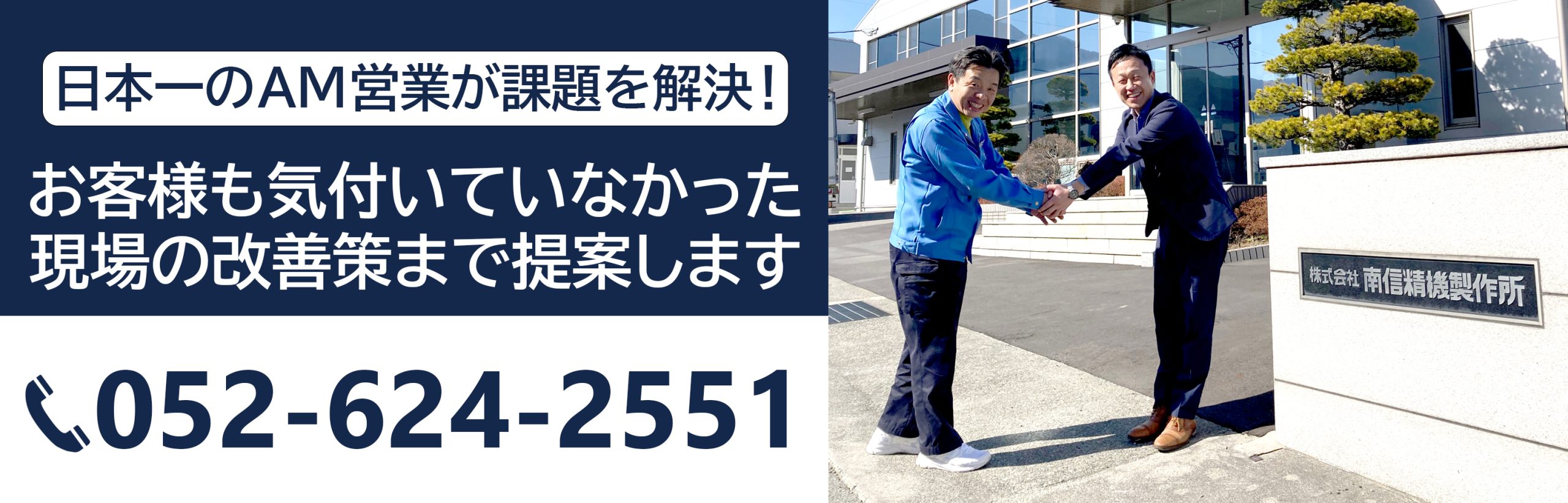